The Impact of Nanotechnology
Nanotechnology, the study and application of extremely small things, has been pivotal for many technological advancements in the past decades. One area of significant impact is in the manufacture of semiconductors, commonly referred to as chips, where manufacturers struggle to increase performance by reducing the size of the fabricated transistors.
By reaching 2nm scale, manufacturers could essentially pack more powerful computing capabilities into a smaller area, translating to better efficiency and improved performance. However, the diminishing size introduces an increase in manufacturing complexity, which in turn significantly inflates the associated production costs.
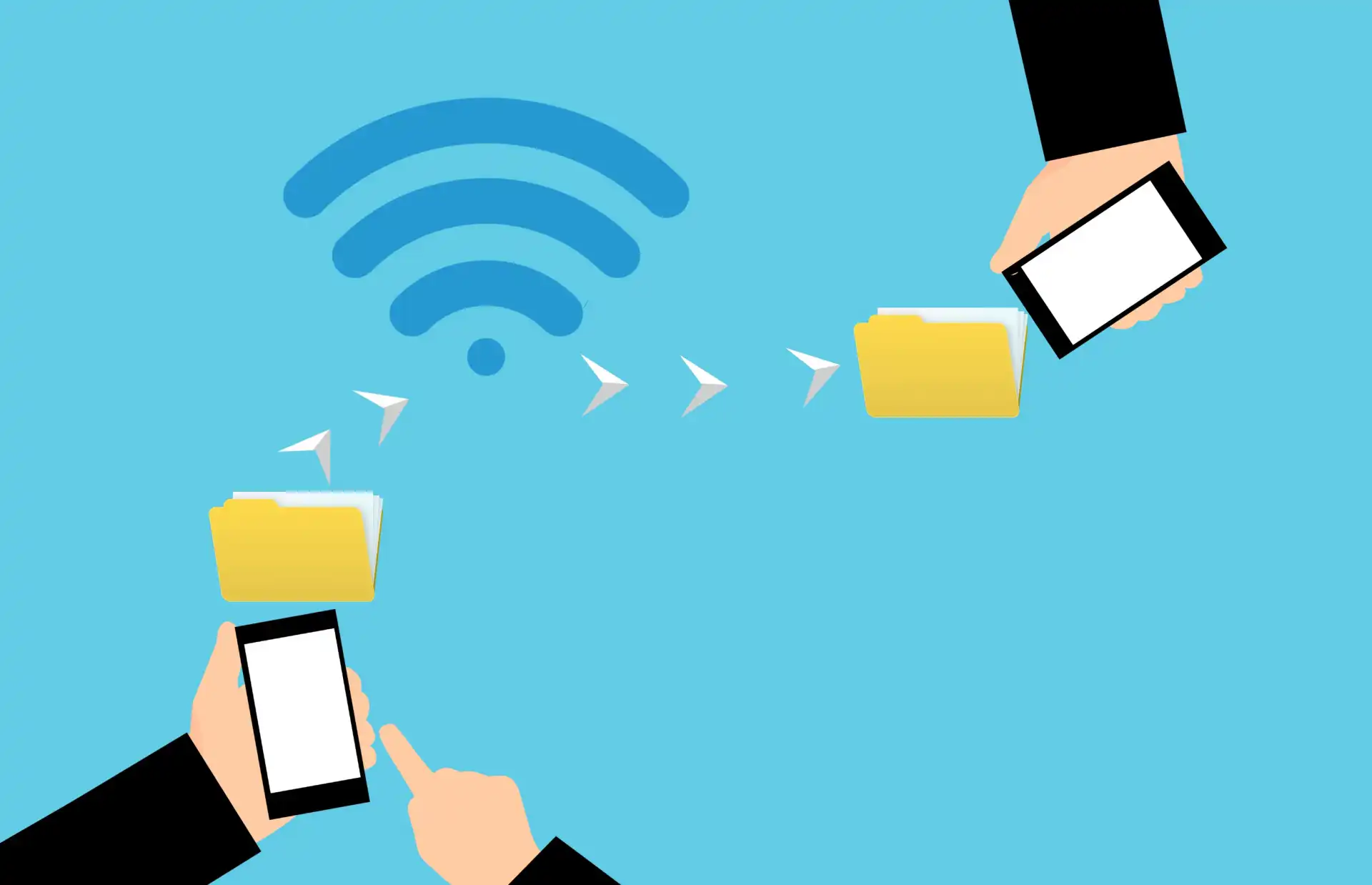
Analysts looking at the semiconductor industry have voiced concerns over the rising costs involved in building a 2nm fabrication facility, predicting a price tag of up to $28 billion. This cost, while challenging to meet, is deemed a necessary expenditure for advancing the frontier of chip technology.
Rising Costs of Semiconductor Manufacturing
Over the past decade, the cost of building chip fabs has been on a steady upward trajectory. Interestingly, this trend parallels the declining size of the chips produced within them. As chip size decreases, the number of transistors packed onto each chip increases, leading to more potent and efficient chips.
However, packing more transistors into a smaller area exponentially increases the complexity of the manufacturing process. It necessitates the need for more advanced, and thus more expensive, manufacturing facilities and equipment. These rising costs shift the dynamics of the semiconductor industry and have led to concerns about prices spiraling out of control.
Analysts predict that production facilities for next-gen chips could cost about $28 billion, with each wafer produced costing around $30,000. This prediction marks a considerable 50% increase in chipmaking costs, painting a challenging picture for the semiconductor industry.
Such predictions stem from the understanding that as chip complexity increases, so does the need for more intricate production facilities replete with cutting-edge equipment.
Addressing the Challenges of Advanced Chip Fabrication
The rising cost of advanced chip fabrication poses a significant barrier to the production of next-gen semiconductors. However, the semiconductor industry is no stranger to such challenges and has historically found ways to circumvent these issues, while continuing to advance the state of chip technology.
Now, faced with this latest challenge, the industry has a multitude of potential responses. One response may be the pursuit of alternative technologies that offer comparable performance benefits but at a lower cost. Another approach may involve creating shared production facilities, hence dividing the costs among multiple parties.
Beyond these, the industry can take a more philosophical approach, turning the problem around and targeting solutions that reduce the complexity of the chips rather than trying to manage it. This method would involve designing chips with fewer transistors, limiting the need for complex and costly production facilities.
However, each of these potential solutions has its own set of challenges and drawbacks to consider. The key will be finding a solution that delivers the necessary improvements while mitigating the cost and complexity involved.
The Future Outlook of the Semiconductor Industry
As the semiconductor industry wrestles with mounting costs and complexities, the future of the sector seems to be at a crossroads. Will manufacturers continue to strive toward ever-smaller chips, despite the escalating price tag? Or will they instead opt for alternative technologies or chip designs with fewer, larger transistors?
No matter which path they choose, the industry is sure to face challenges. As such, the future of the semiconductor industry will likely be defined by a delicate balance – reckoning with the trade-off between the relentless pursuit of technological advancement and the need to control costs and manage production complexities.
Despite this ambiguity, one fact remains clear: the semiconductor industry, like every technology-driven sector, must continue to innovate, adapt, and move forward. In this regard, regardless of the path chosen, the future of the semiconductor industry promises to be an intriguing one, rife with challenges, opportunities, and breakthroughs – as it always has been.
The looming $28 billion cost prediction for a 2nm chip fabrication plant is not only a clear sign of the increasing complexity of manufacturing semiconductors but also a testament to the audacious spirit of the semiconductor industry and its unwavering pursuit of technological progress.